Band Heaters
Customizable
- Home
- »
- Band Heater
Product Catalog
- Immersion Heaters
- Cartridge Heaters
- Air Fryer Heating Element
- Band Heaters
- Casting in Heater
- Finned Heaters
- Flexible heaters
- Immersion Heaters
- Tubular Heating Elements
- Silicon carbide heating elements
- ceramic heating element
- Flange Immersion Heater
- Oven Heating Elements
- Screw Plug Immersion Heater
- Circulation Heater
- Coffee Machine Heating Element
- Duct Heater
- Quartz Infrared Heater
- Water Heater Element
- Boiler Heaters
- Washing Machine Heater
- water heater
- heater strip
- Coil Heaters
- Magnesium oxide rod
- Infrared heater
- Deep fryer heater
- Teflon heater
- Heating Cable
- Plate heat exchanger
- Industrial Oven
- UV Curing Machine
- Water Heater Manufacturers
- PCL Control Box Manufacturer
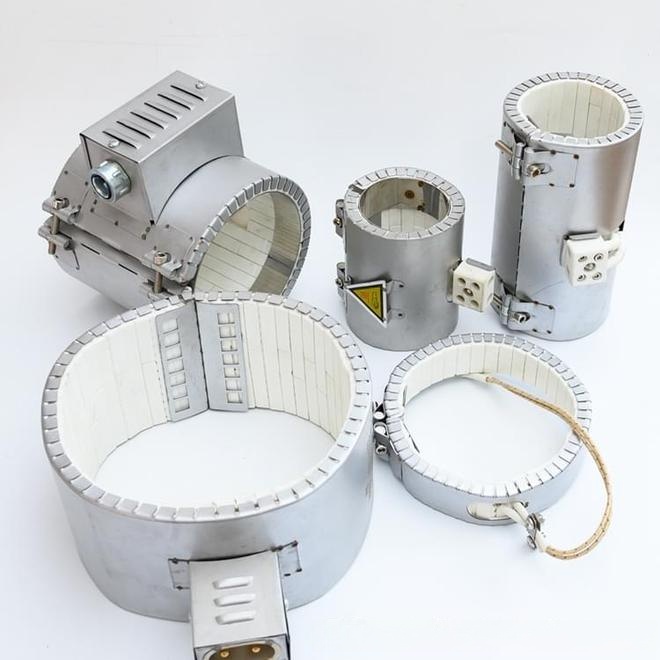
Band Heaters
ELEKHEAT offers a variety of heating solutions primarily designed for cylindrical surfaces, with multiple product lines engineered to deliver reliable performance in diverse operating conditions.
A band heater is a type of electric heating element that is commonly used to heat cylindrical objects, typically in industrial applications. It consists of a metal band, usually made of stainless steel, that is wrapped around the object to be heated. The heater is designed to fit snugly around a cylindrical surface such as pipes, tanks, or other tubular equipment.
Plastic Processing: Heating barrels in extruders and injection molding machines for plastic melting.
Packaging: Used in heat sealing for bags and pouches in packaging machinery.
Food Processing: Heating equipment like chocolate melters and cooking kettles for temperature control.
Metal Processing: Heating barrels or containers for heat treatment and curing metals.
Chemical Processing: Used to heat chemical reactors and mixing tanks for consistent reactions.
Water and Oil Heating: Heating water, oils, and liquids in industrial systems.
Printing: Drying inks and coatings in printing processes.
Renewable Energy: Heating water in solar water heating systems.
Automotive: Battery heating in electric vehicles and energy storage systems.
HVAC and Plumbing: Preventing pipe freezing and maintaining temperatures in hot water systems.
Band Heaters Applications
1.Plastics and Rubber Industry
- Injection molding machines
- Extruders
- Blow molding
2.Packaging Industry
- Heat sealing machines
- Film shrink wrap systems
3.Food and Beverage Industry
- Food processing equipment
- Bottle capping machines
- Industrial ovens
4.Chemical and Pharmaceutical Industry
- Drum heaters
- Reactor vessels
- Tablet presses
5.Printing and Labeling Industry
- Printing rollers
- Labeling machines
6.HVAC Systems and Heating Equipment
- Pipe and duct heaters
- Space heaters
7.Textile Industry
- Fabric curing machines
- Synthetic material processing
Key Features of Band Heaters
Construction: The heating element is usually made from a resistive material such as Nichrome, and it’s wrapped in a metal sheath. The band is typically insulated to enhance heat efficiency.
Operation: Band heaters work by passing an electric current through the resistive material, which generates heat. This heat is transferred directly to the object’s surface around which it is wrapped.
Temperature Control: Many band heaters come with built-in thermostats or are compatible with external controllers to regulate the temperature and prevent overheating.
Customizable: They can be made in different sizes and with various watt densities, making them versatile for different heating needs.
Band Heaters Structure
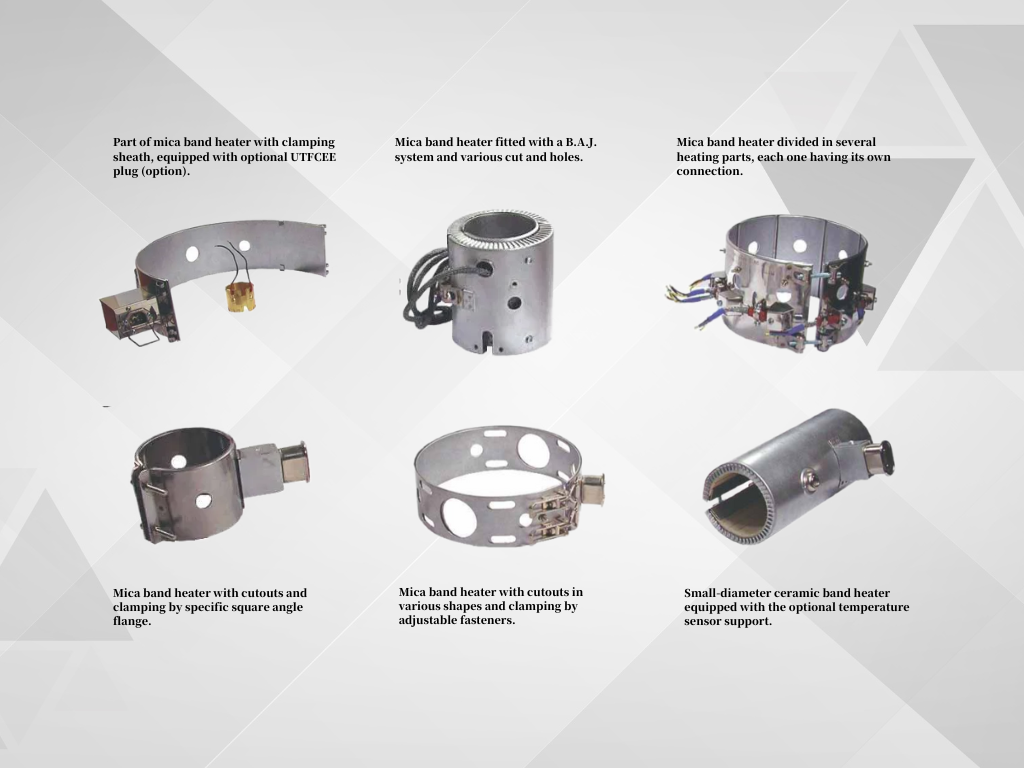
Product Lines
Mica Band Heaters
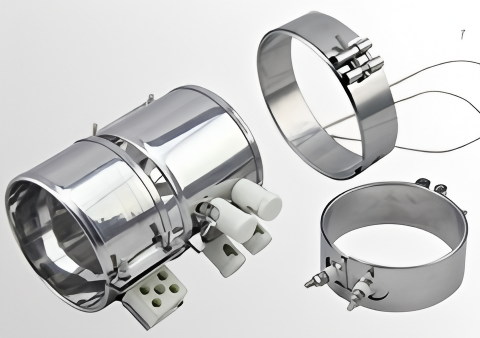
With mica as insulation material and stainless steel as shell, it is a relatively economical and widely used heating coil. The maximum operating temperature is 300℃. The diameter, height and interface size can be customized.
Ceramic Band Heaters
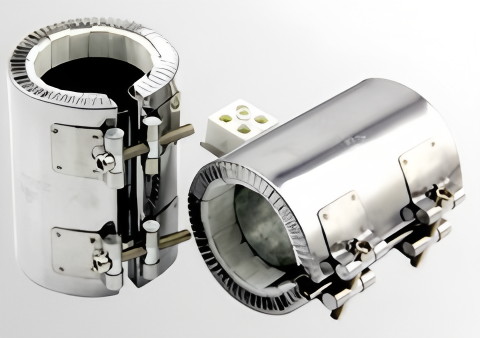
Specially designed high-temperature resistant ceramic tiles are used as insulation materials. Spiral resistance wires pass through the tiles and string them together to form a flexible ceramic heating belt, which is finally encapsulated by a stainless steel shell. The maximum operating temperature can reach 6009C
Quartz Band Heaters
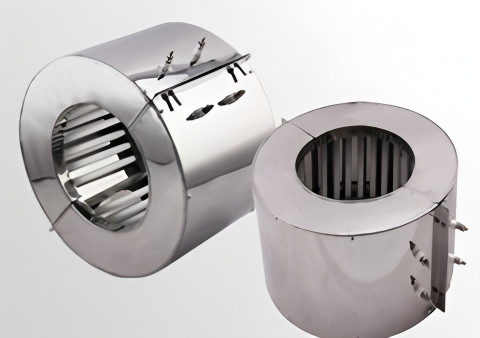
Far infrared quartz electric heating garden is used for radiant heating of tubular objects, with fast heating and high efficiency. The double-piece open structure is easy to install, and the inner diameter, height and voltage power of the product can be customized as required.
Cast Aluminum Band Heaters

The tubular electric heating element is used as the heating element, which is die-cast into the aluminum shell. It has the characteristics of uniform heating, good thermal conductivity, long service life, etc. The maximum operating temperature is 450°C. The product dimensions can be customized.
Band Heaters General Specification
Category | Details |
---|---|
Materials | Sheath: Stainless steel, aluminized steel Insulation: Mica (economical, lightweight), Ceramic (high-temperature, energy-efficient) |
Operating Temperature | Mica Heaters: Up to 300°C (572°F) Ceramic Heaters: Up to 600°C (1112°F) Cast Aluminum Heaters: Up to 450°C (842°F) |
Electrical Specs | Voltage: 120V, 240V, 480V (custom available) Watt Density: Low (<20 W/in²), Medium (20–40 W/in²), High (>40 W/in²) |
Dimensions | Diameter: 1″ to 40″ (custom sizes available) Width: Mica/Ceramic: 1″ to 12″, Cast Aluminum: Up to 24″ Thickness: Mica: 0.5″ to 1″, Ceramic: 0.75″ to 1.5″, Cast Aluminum: 1″ to 3″ |
Clamping Mechanisms | Spring-Loaded Clamps, Latch and Lock Mechanisms, Bolt-On Design |
Features | Integrated Thermocouples, Insulation Jackets (optional), Split Design |
Customization | Shape, voltage, wattage, and dimensions tailored to system requirements |
Why Choose ELEKHEAT Band Heaters?
ELEKHEAT band heaters provide reliable and efficient heating for a wide range of industrial applications. Made with high-quality resistance wire and a durable metal sheath, these heaters ensure optimal heat transfer and long-lasting performance. Their flexible design fits securely around cylindrical surfaces like pipes and tanks, offering uniform heat distribution and energy efficiency. Whether heating liquids, plastics, or other materials, ELEKHEAT band heaters deliver exceptional results. Customizable in wattage, voltage, and temperature controls, they are designed to meet the specific requirements of your heating system. With easy installation and robust construction, ELEKHEAT band heaters are ideal for improving operational efficiency and reducing downtime.
Have a Question?
At ELEKHEAT, we’re here to provide the answers you need. Whether you’re looking for product information, technical specifications, or need assistance with maintenance, our team of experts is ready to help. Don’t hesitate to reach out—we’re committed to ensuring you get the support you need for the best heating solutions.
- Selection Guide
- Installation Guide
- Resource Center
1. Determine Your Application Needs
Precision Heating
Use mica-insulated band heaters for applications needing consistent and controlled heat distribution (e.g., plastic extrusion, injection molding).
For higher precision and minimal heat loss, consider ceramic-insulated band heaters, which provide excellent insulation and energy efficiency.
Rugged and Harsh Environments
Opt for stainless steel sheath band heaters for applications exposed to corrosive environments or where durability is paramount (e.g., food processing, petrochemical industries).
For areas with high vibration or moisture, ceramic band heaters with waterproofing features are ideal.
2. Voltage and Wattage Requirements
Voltage
Match the band heater to your system’s power supply. Common options range from 120V to 480V, with custom voltages available for specific requirements.
Ensure the power source (AC or DC) is compatible with the heater specifications.
Watt Density
Low (<20 W/in²): For heating tasks where gentle heat is required, such as sensitive plastic resins.
Medium (20–40 W/in²): For general-purpose heating, including most extrusion and molding processes.
High (>40 W/in²): For demanding applications, such as heating high-temperature materials or achieving rapid heat-up times.
3. Size and Design
Diameter and Width
Select a band heater diameter that matches your equipment’s cylindrical surface, ensuring a snug fit. Common sizes range from 1” to 40” in diameter.
Choose a width that maximizes surface coverage for efficient heat transfer. Wider heaters distribute heat more evenly over large areas.
Construction Materials
Mica Band Heaters: Thin and lightweight, ideal for applications with limited space.
Ceramic Band Heaters: Offer superior heat retention and energy efficiency, suitable for high-temperature applications.
Insulation and Covering
For energy conservation and operator safety, choose heaters with thermal insulation jackets or heat shields to minimize heat loss and reduce surface temperature.
4. Environmental Factors
Moisture and Chemicals
Use stainless steel-clad heaters with sealed edges to protect against moisture and chemical exposure in harsh environments.
Temperature Extremes
Mica Band Heaters: Operate effectively at temperatures up to 900°F but are best for applications requiring less intense heat.
Ceramic Band Heaters: Handle temperatures up to 1200°F, making them ideal for high-temperature industrial processes.
Heat Dissipation
For high-watt-density applications, ensure proper cooling systems are in place to manage heat dissipation and prevent overheating of the heater and surrounding equipment.
5. Installation and Attachment
Clamping Mechanisms
Mechanism Type | Description | Specifications | Model Recommendations |
---|---|---|---|
Spring-Loaded Clamps | Ensures consistent pressure and accommodates thermal expansion/contraction. | – Material: Stainless steel– Tension: 1–20 lbs– Diameter: 2″–36″ | – ELEKHEAT SL-202 (2″–12″)– ELEKHEAT SL-400 (12″–36″) |
Latch and Lock Mechanisms | Provides quick, tool-free installation and removal, ideal for frequent maintenance. | – Material: Galvanized steel or stainless steel– Locking Angle: 45°–90°– Diameter: 2″–24″ | – ELEKHEAT LL-101 (Standard use)– ELEKHEAT LL-300 (Heavy-duty industrial) |
Attachment Methods
Attachment Type | Description | Specifications | Model Recommendations |
---|---|---|---|
Integrated Thermocouples | Built-in thermocouples for precise temperature control and monitoring. | – Thermocouple Type: J, K, or T– Accuracy: ±1°C– Temperature Range: 0°C to 1200°C | – ELEKHEAT TH-J100 (Type J)– ELEKHEAT TH-K200 (Type K) |
Split-Style Band Heaters | Simplifies installation on existing equipment without requiring disassembly of surrounding parts. | – Split Width: 1″–6″– Diameter: 3″–36″– Material: Mica or ceramic insulation | – ELEKHEAT SP-101 (Mica-based)– ELEKHEAT SP-202 (Ceramic-based) |
Additional Notes:
Spring-Loaded Clamps: Ideal for high-temperature environments where metal surfaces expand significantly, ensuring a tight fit throughout the heating cycle.
Latch and Lock Mechanisms: Preferred for applications requiring frequent access for cleaning or adjustments, such as food processing machinery.
Integrated Thermocouples: Select thermocouples based on system temperature requirements and industry standards (e.g., Type J for moderate heat, Type K for high heat).
Split-Style Heaters: Best for retrofitting or when the equipment cannot be easily disassembled for heater installation.
This detailed table should help you select the appropriate attachment method and clamping mechanism for your specific band heater application. If you need further customization or support, ELEKHEAT can provide tailored solutions.
6. Additional Considerations
Energy Efficiency
Opt for ceramic band heaters with integrated insulation layers to reduce power consumption by up to 30% compared to mica heaters.
Customization
Many manufacturers offer customizable options, including custom shapes, sizes, voltage, and wattage, to suit specialized equipment.
Safety Features
Look for band heaters with grounding terminals and overheat protection mechanisms to ensure safe operation.
Proper installation of band heaters is essential for optimal performance, safety, and longevity. Follow these detailed steps to install band heaters correctly and ensure efficient operation:
1. Pre-Installation Checklist
Inspect the Heater: Check for visible damage to the heater, wiring, or clamping mechanisms. Do not use a damaged heater.
Clean the Surface: Ensure the surface of the barrel, pipe, or cylinder is clean, dry, and free of contaminants, such as grease, oil, or dirt, which can impede heat transfer. Recommended cleaning agents: Isopropyl alcohol or similar solvents.
Verify Specifications: Confirm that the heater’s voltage, wattage, and dimensions meet the application requirements.
2. Tools and Materials Required
Screwdrivers or wrenches (appropriate for clamping mechanisms).
Isopropyl alcohol or cleaning solvent.
Lint-free cloth for surface cleaning.
Torque wrench (for proper clamping tension).
Thermal insulation (optional, to improve efficiency).
Temperature controller (recommended for precise operation).
3. Installation Steps
A. Positioning the Heater
Align the Heater: Place the band heater around the cylindrical surface, ensuring a snug fit without gaps.
Proper Orientation: Ensure that the lead wires or terminals are easily accessible for electrical connection and are positioned away from high-traffic areas or potential hazards.
B. Tightening the Heater
Clamping Mechanism:
Spring-Loaded Clamps: Adjust the clamps evenly to apply consistent pressure around the heater.
Latch and Lock Mechanisms: Secure the latch by locking it at a proper angle (usually 45°–90°).
Torque Settings: Use a torque wrench to tighten clamps uniformly according to the manufacturer’s recommended torque values, typically 10–20 lb-in for standard applications.
C. Thermal Insulation (Optional)
Wrap the heater with a thermal insulation jacket to minimize heat loss and improve energy efficiency.
4. Electrical Connection
A. Verify Compatibility
Check that the power supply voltage and wattage match the heater’s specifications.
B. Connecting Lead Wires
Securely connect the lead wires to the power source using appropriate connectors. Ensure connections are tight and insulated.
For high-temperature environments, use ceramic or fiberglass-insulated wire connectors.
C. Grounding
Properly ground the heater using the designated grounding terminal to prevent electrical hazards.
D. Initial Testing
Conduct a low-power test to ensure the heater operates correctly without overheating or showing signs of malfunction.
5. Operational Guidelines
Temperature Control: Always use a temperature controller or thermostat to regulate heating and prevent overheating.
Thermal Expansion: Account for expansion during operation. Leave slight flexibility in clamps if the heater expands during heating.
Uniform Heating: Ensure no air gaps between the heater and the surface to avoid hot spots.
6. Safety Precautions
Avoid Overlap: Do not overlap band heaters on the surface, as this can cause uneven heating and damage to the heater.
Monitor Temperature: Regularly check the temperature to ensure it stays within the heater’s operating range.
Protect Wires: Keep lead wires away from moving parts, sharp edges, or high-traffic areas to prevent damage.
Power-Off Maintenance: Always disconnect the heater from the power source before performing maintenance or adjustments.
7. Troubleshooting Tips
Issue | Cause | Solution |
---|---|---|
Uneven Heating | Poor surface contact or loose clamps. | Retighten clamps and ensure proper alignment. |
No Heat Output | Faulty electrical connection or power supply. | Verify wiring and test the power source. |
Heater Overheating | Lack of temperature control. | Install a temperature controller or thermostat. |
8. Maintenance and Removal
Maintenance
Inspect regularly for signs of wear, damage, or loosening of clamps.
Clean gently with a damp cloth to remove residue; avoid abrasive materials.
Periodically check electrical connections for tightness and integrity.
Removal
Clamping Mechanisms: Loosen clamps or latches carefully to avoid damaging the heater or surface.
Heater Removal: Gently slide the heater off the surface, ensuring lead wires are disconnected beforehand.
Cleaning the Surface: Remove any residual debris or oxidation with a lint-free cloth and isopropyl alcohol before installing a new heater.
By following these steps, you can ensure the proper installation and maintenance of your band heaters, maximizing their performance and lifespan. If you need further assistance or technical support, contact ELEKHEAT for expert guidance!
Welcome to Elekheat Resource Center, your one-stop destination for comprehensive technical documentation and industry insights. Designed to support professionals across various sectors, our resource hub provides access to valuable information.